Evolution of the bus body
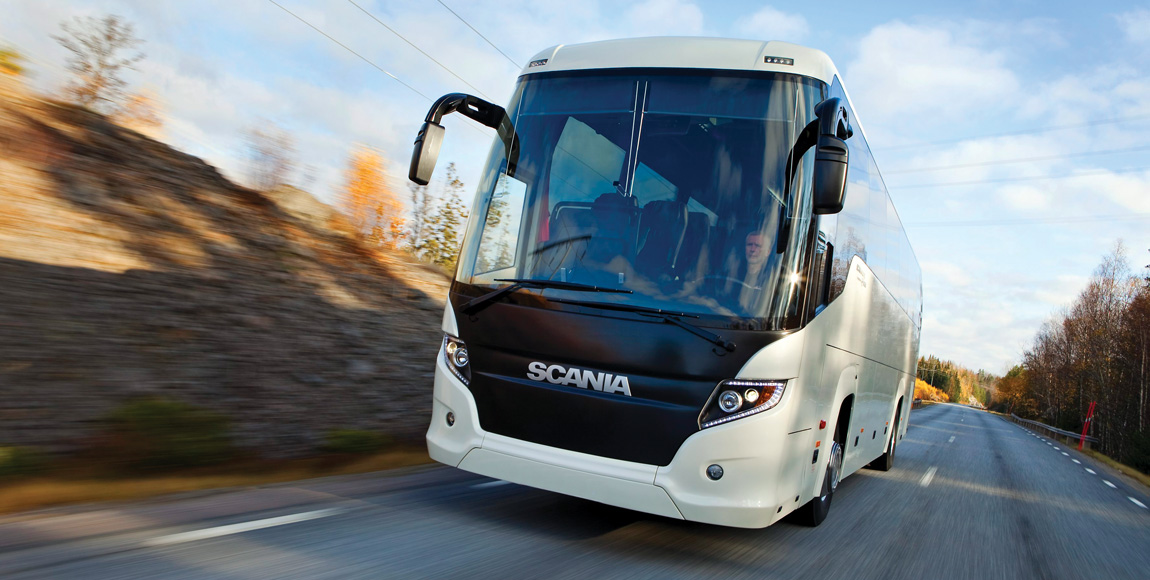
Front and rear modules of modern buses are two of the most visible indicators of styling changes in the sector โ but transformation has occurred in other areas of the structure, too
South Africaโs bus and coach industry is perceived to be a dynamic and challenging environment, constantly evolving to accommodate the needs of bus and coach operators who demand lower running costs, even lower repair bills, extended maintenance and service schedules, as well as improved reliability and durability from their vehicles.
Additionally, in recent years government legislation globally has been aimed at reducing vehicle emissions and improving passenger and driver safety, encouraging bus builders around the world to rethink methods of manufacture in order to meet stringent, ever-tightening regulations.
From this perspective, many local constructors have begun to utilise a wide range of new materials and processes in the manufacturing of bus bodies. Component stiffness, crash resistance, as well as the elimination of noise, vibration and harshness both inside and outside of the vehicle, have all become important aspects of bus building.
In terms of body make-up, many local constructors are making increased use of lighter, stronger, steel, aluminium or alloy, drawing on the expertise of international parent companies to ensure the best structural standards and using latest anti-corrosion processes to help to protect metal elements from damage. For a similar reason, greater use is being made of advanced composites for structural applications.
Roof assemblies of modern bus and coach vehicles face particularly tough challenges. Apart from obvious requirements of long-term structural integrity and durability, additional provisions include lowest possible weight to improve vehicle handling and fuel economy, highest possible strength with regard to roll-over resistance and occupant safety, and increased functionality regarding the accommodation of items such as air-conditioning units or sunroof apertures.
Comfort and safety, along with an ability to perform perfectly no matter what the weather conditions, is what passengers have come to expect from a bus. Enhanced aesthetics and aerodynamics have become more important to them, too โ and itโs no surprise that even the most basic of commuter vehicles have begun to incorporate these aspects into their designs, as the past ten years have seen a dramatic improvement in the styling of buses and coaches.
Front and rear modules of modern vehicles are two of the most visible indicators of transformation. The use of thermoset composites instead of steel is now common for such applications, and has resulted in dramatic alterations in aerodynamic performance, with benefits felt in reduced fuel consumption.
However, itโs not only styling that has undergone significant change. Applications must still meet ever-tougher durability, impact and ease-of-build requirements, marking a shift in some quarters to bonded assemblies โ which enable weight reduction versus mechanically fastened systems โ again resulting in better fuel economy and lower emissions.
Further, the use of adhesives and sealants has been shown to help to prevent corrosion of metal parts, reducing the need for repair. Also, apart from offering improved resistance to water leakage, adhesive systems are said to be instrumental in absorbing vibration, helping to lower interior noise levels.
Predicted trends for front and rear mask applications in the bus manufacturing industry include increased use of advanced composites and the possible use of thermoplastic composites such as glass-mat reinforced thermoplastic composite (GMT) and long-fibre injection (LFI).
In addition, bus operators have driven a trend towards increased interior comfort and functionality in recent years, requiring the use of a diverse mix of interior plastics, fabrics and other materials to keep passengers relaxed yet secure in the cabin environment. Performance requirements for interior components have increased, too, with higher operational wear and tear prerequisites, improved environmental performance needs, lighter weight and reduced cost.
According to bus construction experts, the general trend is towards greater use of polypropylene composites; the implementation of higher occupant impact-protection standards; greater restrictions on the use of materials containing solvents and volatile organic compounds; enhanced recycling requirements; and stricter interior and exterior noise, vibration and harshness limits.
Connectivity and other electronic features are beginning to play a significant role, too, in the life of a bus, with many that ply long-distance routes incorporating Wi-Fi, USB ports at every seat, GPS systems for navigation and cruise control for open-road travelling. Television monitors, audio systems, reading lights and even refrigeration systems to keep drinks cool are commonplace.
On the subject of cooling, windows on commuters of the long-distance sort tend to be bonded, tempered and tinted, adding stylistic and aerodynamic appeal and effectively helping to reduce heat build-up in the cabin โ all of which helps to point to the fact that todayโs bus bodies have come a long, long way.
Published by
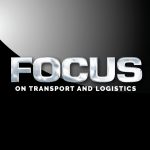
Focus on Transport
focusmagsa
